Bolted Flange Design
This is the documentation page for the Bolted Flange Design module. You'll find here everything you need to understand how to use our application.
1. Types
2. Drawing
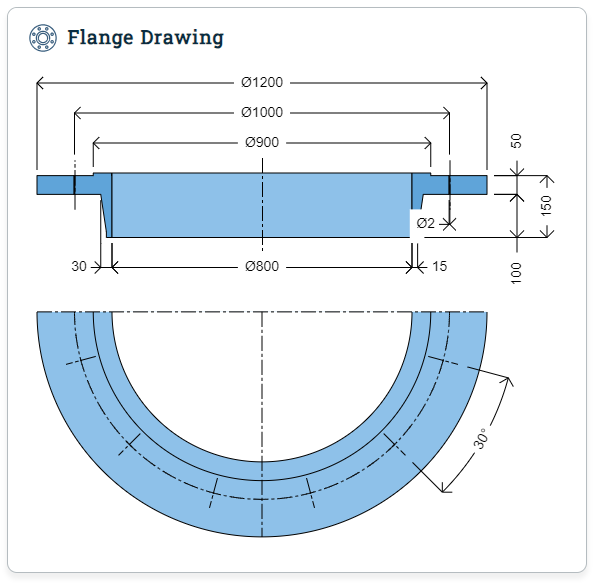
The Bolted Flange Design module can dynamically generate the flange drawing as the User fill the dimensions fields. It follows the flange types and figures shown in ASME BPVC Section VIII Division 1 Appendix 2[ 1 ]. If there's some inconsistency in the dimensions, an red warning will be shown instead of the drawing. Fixing the inconsistency will make the drawing to be shown again.
Fig. 1.1 below show an example of flange drawing. For now, only the frontal cross-section and top view will be shown, but we're working to also show the bolts and gasket drawing.
3. Units
For now (version 1.0.0), only International Unit System[ 2 ] or just SI Units is accepted, but we're working to implement the Imperial Unit System[ 3 ] in the following versions, as it's still used by many countries (specially USA) and companies.
4. Fields
Below is a list of all the available fields in the Bolted Flange Design module. Not all fields are shown at once, some fields are unique for some types of flange, as hub fields, that only show for flanges with hub.
Other fields are shown, but can only be edited if certain condition are met, as the material fields, which can only be edited if the User selected the checkbox "Use your own values?".
4.1. Module
The module tab have two versions: one for a new part (see Fig. 4.1.1) and one for an existing part (see Fig. 4.1.2). The difference is that when a part is saved, an unique identifier (ID) will be generated for it and it can be linked to other parts and equipment. The ID is shown above the Module tab (see Fig. 4.1.3) and there's a button to Project Management module beside it.
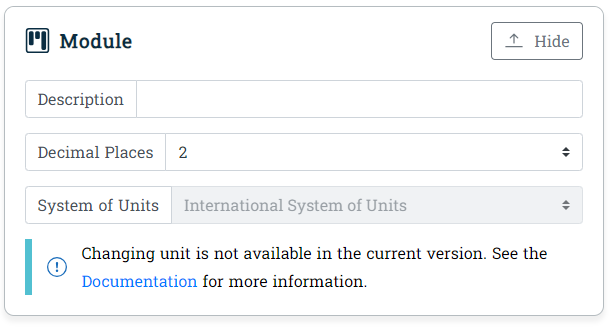
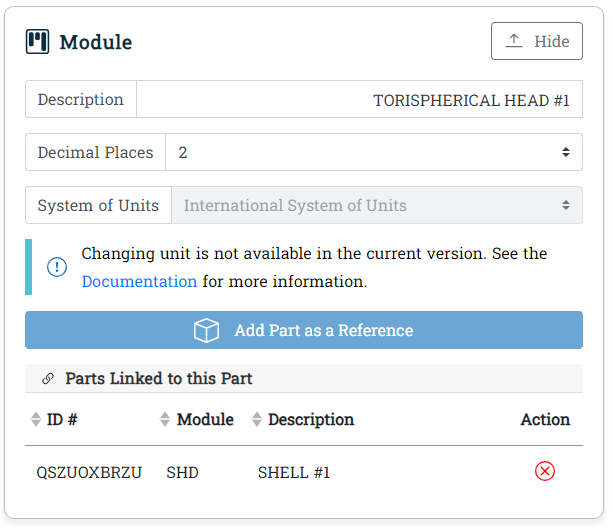

Variable | Name | Unit | Type | Description |
---|---|---|---|---|
<none> | Description | <none> | Input | Short description of the part. For example: if designing a Bolted Flange to be connected at the upper part of the vessel, you can simply call if Upper Flange, if there's other flanges in there, you can be even more specific, calling if Upper Left Flange or Upper Gas Flange. Just remember that you'll use the description to identify the part (you can also use its id, but it's usually difficult to remember) |
<none> | Decimal Places | <none> | Select | Number of decimal places to be used in the calculations and results. User can choose between 1 to 4 decimal places (also known as precision). |
<none> | System of Units | <none> | Select | Unit system that will define the units used in all the variables in the calculation. The most known types are Imperial System and International System. Unfortunately we still don't support changing units and the International System will be used as a default. |
4.2. Process
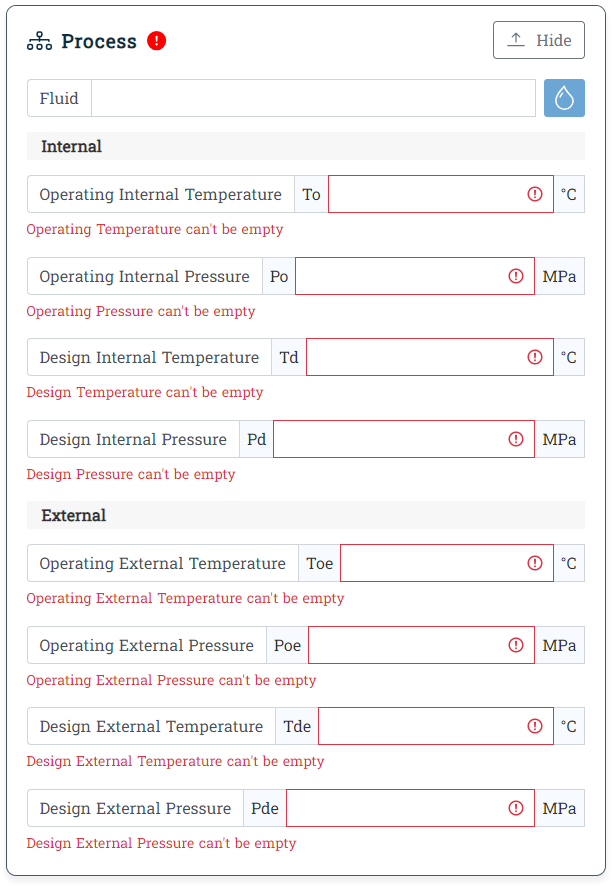
Variable | Name | Unit | Type | Description |
---|---|---|---|---|
<none> | Fluid | <none> | Fluid name, it's optional as it will not be used in any calculation. See Note (2). | |
To | Operating Temperature | °C, °F | Temperature of the vessel when the equipment is in service. It's optional. See ASME BPVC Section VIII Division 1 Nonmandatory Appendix C for suggested methods to obtain the operating temperature of vessel walls in service and also UG-20 for more information. | |
Po | Operating Pressure | MPa, PSi | Pressure of the vessel when it's in service. It's optional and will not be used in any calculation. | |
Td | Design Temperature | °C, °F | Maximum expected temperature in the vessel in normal operation. See UG-20 for more information. | |
Pd | Design Pressure | MPa, PSi | Maximum expected pressure in the vessel in normal operation. See UG-21 for more information. |
4.3. Dimensions
Variable | Name | Unit | Type | Description |
---|---|---|---|---|
<none> | Flange Type | <none> | types according to Figure 2-4 from ASME BPVC Section VIII Division 1. Although 24 types are shown in the Code, we only support 22, the 2 remaining are Flanges with Nut Stops. The User will notice that some types have exactly same information (including drawing) as other types (it's the case of Fig. 2-4(9) and Fig. 2-4(10)) and we did it because we wanted to stay true to the Code, letting the User selected the figure used in the project. Other softwares decided to only let the User choose between Integral and Loose type of flanges, without mentioning the figures. | |
<none> | Flange Construction | <none> | construction type according to Figure 2-4. It can be either Integral or Loose. There are Optional types (Figures 2-4(8) to 2-4(11)) which let the User selected if it'll be calculated as Integral or Loose. | |
B | Flange Inside Diameter | mm, in | inside diameter of flange. When it's less than 20∗g1 it will be optional for the designer to substitute B1 for B in the formula for longitudinal stress SH | |
A | Flange Outside Diameter | mm, in | Outside diameter of the flange, it's the biggest dimension of it. | |
t | Flange Thickness | mm, in | Thickness of the flange, the most important variable. | |
tn | Nozzle Wall Thickness | mm, in | Nominal thickness of shell or nozzle wall to which flange or lap is attached | |
g0 | Thickness of Hub at Small End | mm, in | Thickness of the part of the hub that is farther from the flange. | |
g1 | Thickness of Hub at Back of Flange | mm, in | Thickness of the part of the hub that is closest to the flange. | |
h | Hub Length | mm, in | Hub length, used only in flange types that have hub, as Fig. 2-4(8a) and Fig. 2-4(10a). | |
faceID | Flange Face Inside Diameter | mm, in | Inside diameter of the face used to seat the gasket. | |
faceOD | Flange Face Outside Diameter | mm, in | Outside diameter of the face used to seat the gasket. In the drawing it's shown as a raised face but, in fact, it can be a flat face, as shown in the Figure 2-4. | |
pd | Inside Pipe Diameter | mm, in | Dimension only used when User selected flange types that have pipes attached (Fig. 2-4(2), 2-4(2a), 2-4(3), 2-4(3a), 2-4(4), 2-4(4a), 2-4(4b) and 2-4(4c), 2-4(8), 2-4(8a), 2-4(9), 2-4(9a), 2-4(10), 2-4(10a) and 2-4(11)). The sole purpose of this dimension is to be used to draw the pipe inside de flange, it will not be used in any calculation, so the pipe required thickness will not be calculated. If the User want to calculate it, use the Shell & Head Design or use a standard pipe. | |
tl | Lap Outside Diameter | mm, in | Dimension only used when User selected lap flange types (Fig. 2-4(1), and 2-4(1a)) | |
corr | Corrosion Allowance | mm, in | It's up to the designer engineer to define a corrosion margin or corrosion allowance for the project (see UG-25 from ASME BPVC Section VIII Division 1). Our application will show the maximum allowable pressure for both conditions (new and corroded) | |
<none> | Use B1 instead of B | <none> | As described in the variable B above, when B is less than 20*g1, the user can use B1 instead of B for longitudinal stress (SH) |
4.4. Bolting
Variable | Name | Unit | Type | Description |
---|---|---|---|---|
<nome> | Do you want to insert your own values? | <none> | When checked, will let User edit the fields Bolt Outside Diameter and Bolt Root Area and will hide the fields Standard and Bolt Size and Class. | |
<none> | Standard | <none> | List of standard codes for bolts and screws. When a code is selected, the Bolt Size and Class field will load all available sizes for the selected code. | |
<none> | Bolt Size and Class | <none> | List of all available bolt or screw size for the selected standard code. | |
C | Bolt Circle Diameter | mm, in | Circle where bolts will be located. | |
BOD | Bolt Outside Diameter | mm, in | Outside diameter of the bolt (do not get confused with root diameter). This field is automatically filled when User select a bolt size from Bolt Size and Class field. | |
BA | Bolt Root Area | mm^2, in^2 | Root area of the bolt (don't use bolt outside diameter to find its area). This field is automatically filled when User select a bolt size from Bolt Size and Class field. | |
N | Number of Bolts | <none> | It's a good practice to use multiple of 4 as the number of bolts but the application will allow any integer (decimal not acceptable). |
4.5. Gasket
Variable | Name | Unit | Type | Description |
---|---|---|---|---|
<none> | Select Gasket from Database? | <none> | ||
gt | Gasket Thickness | mm, in | ||
GID | Gasket Inside Diameter | mm, in | ||
GOD | Gasket Outside Diameter | mm, in | ||
m | Gasket Factor | <none> | ||
gy | Gasket or Joint Surface Unit Seating Load | MPa, psi | ||
ff | Flange Facing Sketch (Table 2-5.2) | <none> | ||
ffc | Column from Table 2-5.2 | <none> |
4.6. Material
Variable | Name | Unit | Type | Description |
---|---|---|---|---|
<none> | Is the Material Normalized? | <none> | ||
<none> | Use your own values? | <none> | ||
<none> | Material Name | <none> | ||
Suf, Sub | Tensile Strength at Design Temperature | MPa, psi | ||
Syf, Syb | Yield Strength at Design Temperature | MPa, psi | ||
Emdf, Emdb | Elastic Modulus at Design Temperature | MPa, psi | ||
Sf, Sb | Allowable Stress at Design Temperature | MPa, psi | ||
Saf, Sab | Allowable Stress at Ambient Temperature | MPa, psi | ||
mdf, mdb | Material Density | kg/m^3, lb/ft^3 | ||
<none> | Group Number | <none> | ||
<none> | P-Number | <none> | ||
<none> | P-Number Thickness | mm, in | ||
<none> | External Pressure Chart | <none> | ||
<none> | UCS-66 Curve | <none> |
4.7. Settings
Variable | Name | Unit | Type | Description |
---|---|---|---|---|
mdmt | Minimum Design Metal Temperature | °C, °F | ||
<none> | Show factors calculation? | <none> | Show flange factors equations according to Table 2-7.1 and its results in the results page. As there's 45 equations, the results page and the calculation report can get quite long, so we advice you to show it only if needed (for checking or when requested by Customer) | |
<none> | What Test specification should be used? | <none> | Select the type of test that will be performed in the pressure vessel. It can be according to UG-99(b), UG-99(c) or UG-100. Each option have it's own equation, so you can't calculated according to UG-100 and perform the test according to UG-99(b). | |
<none> | Disable sharing of this Module? | <none> | When set to Yes, you'll be able to share this Module/Part with other Users and they can request access to it. You can also change this option at the Project Management module. |
5. Messages
The Module will show messages in the results pages when needed, these messages can be either warnings or info.
5.1. Warnings
If there's any error in the calculation a red warning message (see Fig. 4.1) will be shown in the results page. The warning will have information regarding the error to help User fix it and, if the GoTo link is clicked, the equation with error will be shown.
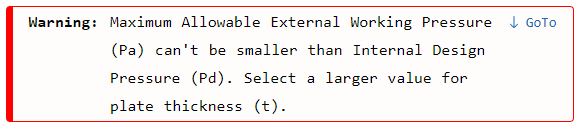
The User will still be able to save the Module even though there's a warning message. We decided to keep this way because, sometimes people don't want to fix things right away or wan't to let other people deal with it (just share the Module with other User using our Project Management module)
5.2. Info
6. Sharing
The sharing option is something that we thought would be useful because engineers works as a team and usually share their projects with another engineers or customers, either to review or for approval.
Nowadays working side by side (physically) with other engineers is becoming something from the past. Hybrid and Remote position are becoming common in many companies. So no more printing the project and let in the co-work table to be checked. You either send the PDF (or software file) by e-mail or save it in the company drive.
Our approach is a little bit better. We let the USER choose which USERs can access the project, equipment and part and what kind of permission they will have. You can let some USERs change anything in a Part or let they only see it (input and output).
To share a project, equipment or part you must be its owner. You can be the owner by either creating the project, equipment or part or if the current owner delegates it to you. Also the option Disable sharing of this Part? in the Settings tab must be set to No (see Fig. 4.5.1.), in case of Part and if it's a Project or Equipment, the sharing button in the PJM module must be set to enable (see more about it in the Project Management documentation).
Currently there are two types of sharing status:
- Full Access: this type of access let the USER make changes to the Project, Equipment and Part but can't delete it (only its owner can do that)
- View Access: USER with this type of access can't make changes, can only see the input and output data.
7. Limitations
The version comes with some limitations which are listed below:
- Flange with Nut-Stops (2-12) not available.
- Reverse Flanges (2-13) not available.
- 3D Model not available.
8. Results
8.1. Summary
The Summary (see Fig. 9.1.1.) shows the most important information from the results. It also shows if there's some error in the calculation (it'll be shown in red).
In the future version we'll let the User select which information want to see in it.
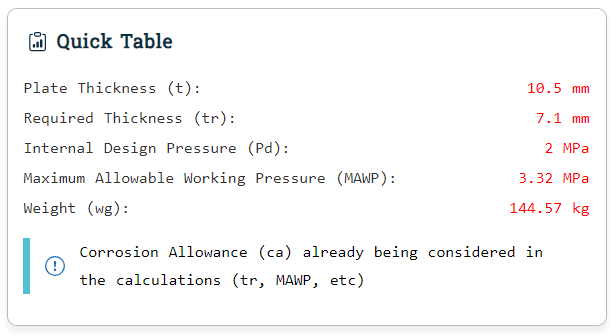
8.2. Input
The Input tab (see Fig. 9.2.1.) in the results page shows all the information from the input page. It can be used to check all the data inserted by the User and by our system. The input will also be shown in the Calculation Report (DOCX).
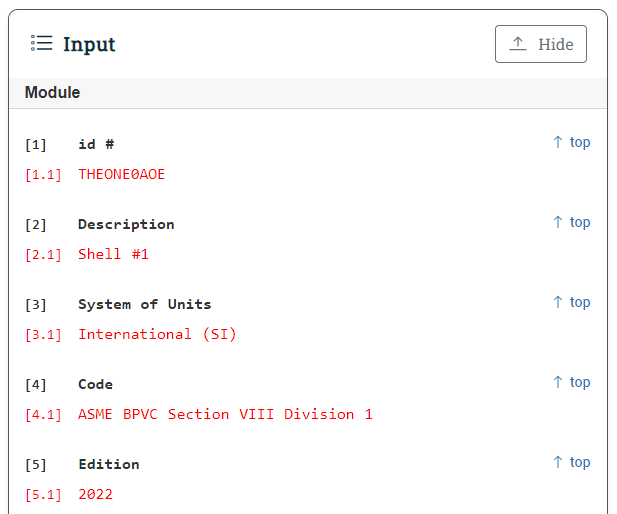
9.3. Output
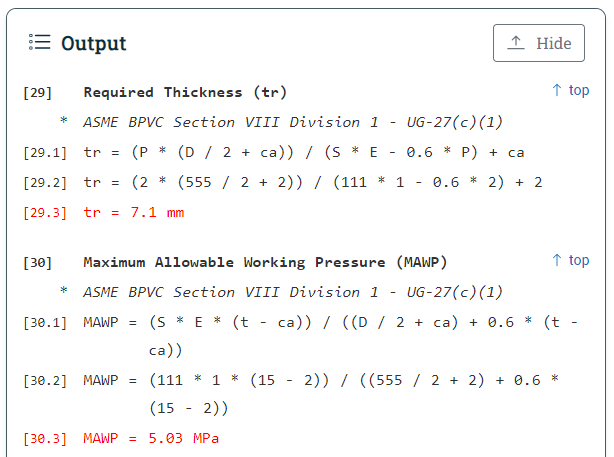
9.4. Bottom Menu
At the bottom of the page you'll find three buttons (see Fig. 9.4.1.):
- Back: will bring the USER back to the Input page
- Save: will save the Part and the USER will be able to access it using the direct link shown in the browser or through the Project Management module
- Report: will generate and download the Calculation Report

9.5. Summary
To help USER easily check the equations and input data we created a summary which is show at the right side of the page (see Fig. 9.5.1.). It's composed by hyperlinks and if clicked the part where the item is located will be show. The list is divided in Input and Output to facilitate the identification.
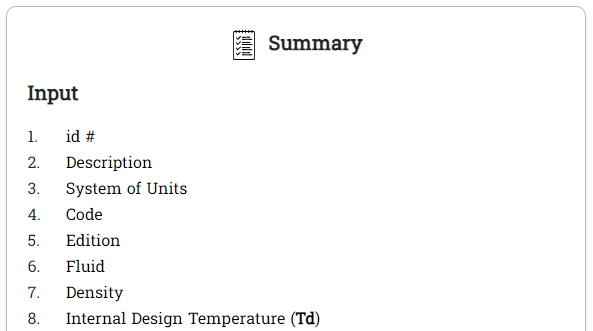
9. Testing
If you access the Bolted Flange Design module without being logged, you'll see a warning message as shown in the Fig. 10.1. stating that you're entering into a testing environment, which basically means that you'll not be able to use it in a real case, as some features are disabled and the data range that can be use is limited.
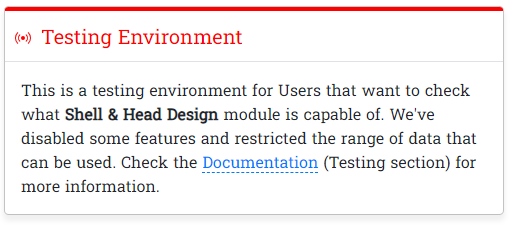
If you need to use the it beyond its testing limitation, contact us through Contact page and we'll see what can we do for you. We could, for example, give you a 1 day free trial or a guided testing with us.
9.1. Limitations
There are two types of limitation in the Testing Environment: features disabled and data range restriction.
9.1.1. Features Disabled
9.1.2. Data Range Restriction
9.2. Access Protection
The public API used in the testing environment is different from the API used in the production environment. So, even if someone tries to direct access the API with values outside the data range, the API will return an error.
10. Linking Parts
The calculation modules that we've in the ΣCalc or, more specifically, in the MarsCalc package, works independently from each other. It means that, if you are designing a spherical head to be attached in a conical shell, one part will not "know" about the other. The only exception are the modules that require the USER to load data from other modules. It's the case for Opening Reinforcement Design (ORD) and Saddle Support Design (SSD).
To let the USER specify which parts are connected, we created the reference list. Let say, for example, that you have a torispherical head connected to a cylindrical shell. If you go to the Equipment tab in the Project Management module you'll see that the equipment have many parts, including the head and shell specified above but, you can't know how they are connected. If you add the cylindrical shell as a reference to the torispherical head, you'll know that it's connected.
The problem now is: what if the cylindrical shell have two heads, how can you know which one is in the top and which is in the bottom? Unfortunately we don't have a way to specify that, we're planning to let USER to assembly the pressure vessel just like PVElite does (using 2D drawings and nodes to connect the parts) but it isn't our top priority (it is listed in the Pool of Ideas with the ID # 9FF565B5)
Okay, lets go to the how to part. To add a part as a reference, first make sure that both parts are saved (exist and have and ID), then click in the Add part as a Reference (see Fig. 4.1.2) button. A modal (see Fig. 11.1) will be shown with the list of all parts created by the USER. If there are too many parts and you already know the ID of the part that you which to add, just type it in the search field to filter the list. To finish, just click in the part that you want to add and the modal will close and it'll appear in the Parts Linked to this Part table in the Module tab.
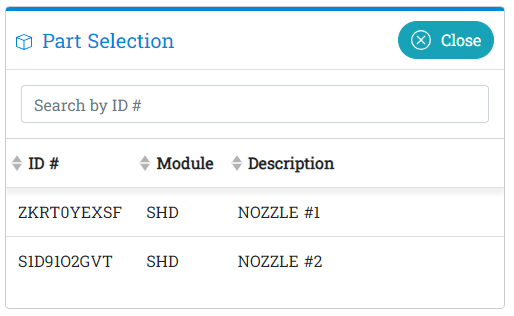
One important thing that you must understand: linked parts have no effect in the calculation. It serves only as a reference. So if you add a stainless steel part to a carbon steel, the application won't show any warning.
11. Calculation Report
Calculation report can be generated and downloaded by clicking on the Report button located in the bottom menu, which is only visible in the results page. The file name will be the part ID.
Fig. 11.1. shows the information contained in the first page of the report. Company name and logo can be set in the Dashboard. All the other information are automatically generated.
The second page will show the part description (information given by the USER in the Module tab), part id (automatically generated), drawing (same as shown in the input page), input and output (equations).
Changelog (doc)
If you want to receive an e-mail notification every time an article or documentation is updated, just sign up and click in the Notify Me button at the bottom of the page (only visible for logged USERs).